Effective inventory management is important for any business that handles physical products. It ensures you have the right amount of inventory on hand to meet demand without overspending on additional inventory. Implementing the best inventory management practices can help companies increase productivity, cut expenses, and generate more profits.
What are the best practices for inventory management?
Best inventory management practices are strategies and guidelines for businesses to manage and control materials, parts, and consumables used in production processes.
These practices can help companies maintain optimal inventory levels by avoiding the costs of storing too many items or purchasing more inventory items than needed. Having a set of best practices streamlines operations and decision-making based on industry-recognized standards and guidelines.
Optimizing inventory management processes is crucial for any business to maximize profits, as the purchase, organization, and use of inventory items can have a significant impact on profits. This article explains the importance of inventory management and 5 best practices.
Top 10 Best Practices for Effective Inventory Management
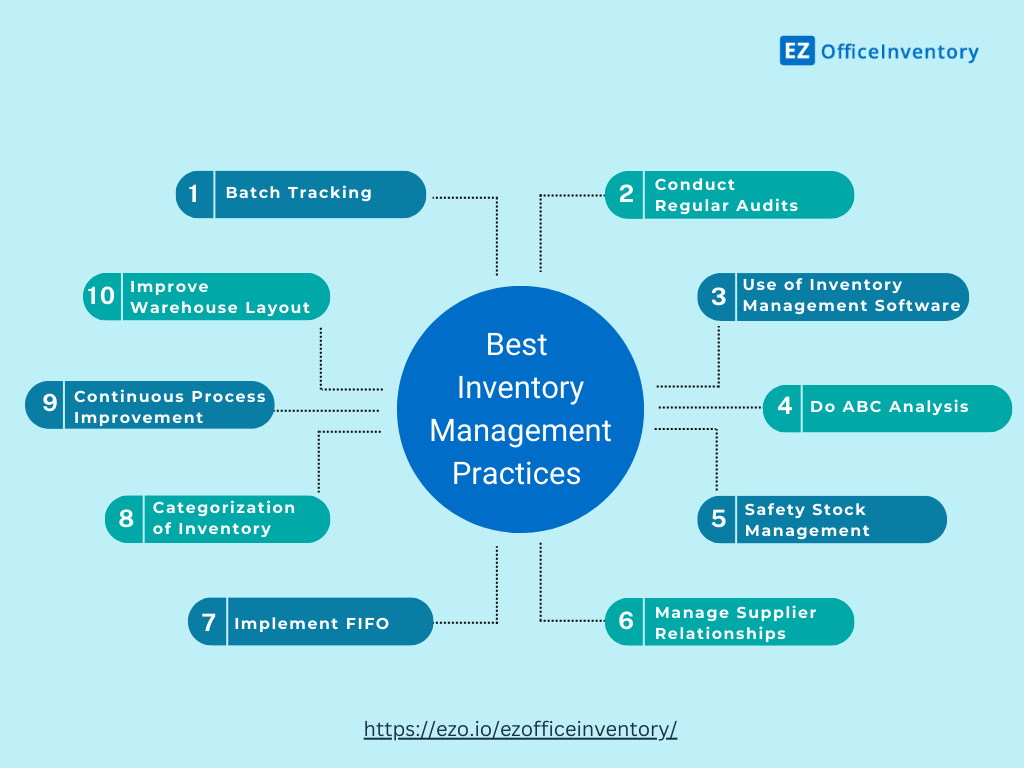
Here are 10 key inventory management practices every business should adopt:
1. Batch tracking
Assigning a unique batch number or allocation code during receipt allows tracking of inventory by specific batches and purchase orders. This identifies production dates, expiration dates and facilitates targeted recalls or quality control of problematic batches.
Batch tracking allows traceability of specific batches and allows the implementation of a FIFO approach. It also links inventory ledgers, purchase orders, and material batches for end-to-end tracking.
2. Implement first-in, first-out
Based on the date of receipt, the oldest inventory items are used first to reduce losses caused by product expiration and obsolescence.
This inventory management tip can also help you maintain the freshness of perishable items in your inventory. Following the first-in, first-out principle provides the most accurate inventory assessment for accounting purposes. First-in-first-out should be combined with batch tracking to facilitate identification of receipt dates.
3. Regular review
Performing regular, comprehensive physical inventory counts and comparing the counts to balances in inventory records can help identify discrepancies and discrepancies. Regular cycle counts highlight inventory losses due to damage, expiration, theft, or write-off errors.
It ensures that the inventory management system reflects the actual inventory on hand. Conducting an audit also provides an audit trail that helps prevent inventory misplacement.
4. Use inventory management software
Centralized digital systems for managing inventory, orders, shipments and other transactions provide real-time visibility into inventory levels across the supply chain.
Inventory management software automates routine processes, minimizing errors and delays. It generates insightful reports to enable data-driven decisions around inventory. The unified system integrates accounting, sales order, purchasing and other functions, and information flows smoothly.
5. Perform ABC analysis
ABC analysis involves classifying inventory into categories A, B, and C based on annual consumption values. Item A, which accounts for 70-80% of the total inventory, needs to be strictly controlled and focused.
Option B requires less supervision and receives a moderate level of attention and resources. C projects require minimal management attention because they represent only a small portion of the total value. This targeted approach focuses resources where they can have the greatest impact.
6. Safety stock management
Determining optimal safety stock levels can provide a buffer against uncertainty in demand and changes in supply delivery lead times. Historical sales patterns and demand forecasts help establish required safety stock levels. The goal is to avoid stockouts, but also avoid overstocking. Replenishment cycles can be derived from agreed or projected order frequencies and delivery times.
7. Manage supplier relationships
By strategically developing partnerships with reliable suppliers, long-term contracts can be negotiated that provide guaranteed supply and stable prices. Involving suppliers early on in product design as well as inventory and production planning allows for better coordination. Shared demand forecasts further facilitate synchronization strategies. Inventory costs can be optimized through methods such as vendor-managed inventory.
8. Inventory classification
Segmenting inventory into raw materials, work-in-progress, finished goods, and returnable, consumables enables the application of customized management practices that best suit the characteristics of each category.
For example, finished goods may require demand forecasting and sales order tracking, while raw materials focus on replenishment times and supply lead times.
9. Continuous process improvement
Regularly reviewing and refining inventory management processes using methods such as lean, just-in-time models and advanced automation tools can help identify problem areas. Areas of waste or non-value activity can be addressed and eliminated.
Improving workflows, storage layouts, procedures and key metrics can improve overall inventory performance. Small, consistent improvements can lead to significant efficiency gains over time. It also ensures that inventory practices keep pace with changing business needs.
10. Improve warehouse layout
A good warehouse layout improves inventory traceability, space utilization, order fulfillment and inventory accuracy. Material movement and picking efficiency can be improved by designing warehouse layouts based on inventory velocity or frequency of access.
Faster-moving items should be stored closer to the shipping area, while slower-moving items should be stored further away.
Standardization of logical layout within and between warehouses is key. Ensure inventory labels and signage are highly visible.
Why is it important to follow inventory management best practices?
Following best practices for managing inventory is critical for several reasons:
Optimize inventory costs
In order to reduce unnecessary carrying costs, inventory levels must be optimized. Keeping extra inventory unused ties up working capital and increases costs related to handling, storage, insurance, taxes and other costs.
Overstocking can be prevented by closely coordinating inventory purchases with actual consumer demand. Deloitte claims that by implementing best practices, companies can reduce inventory holding costs by up to 20%.
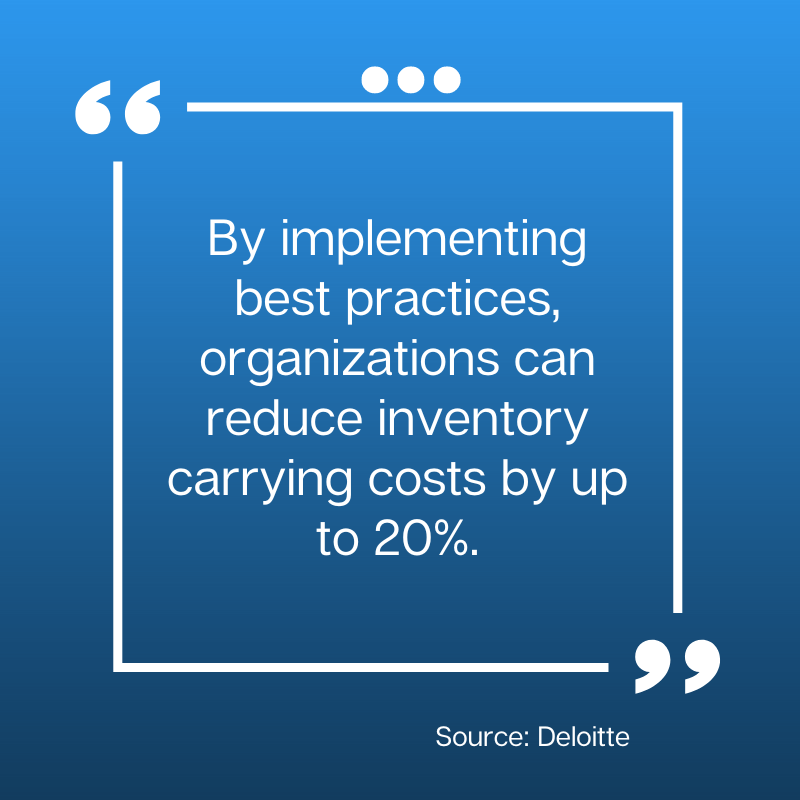
Leveraging inventory management automation can minimize overall inventory holding costs. Modern cloud-based inventory management software provides businesses with real-time inventory visibility so that they can maintain inventory levels at optimal levels. The ability to maintain inventory levels at optimal levels frees up working capital for other business purposes.
Provide actionable data
Inventory analytics provide valuable insights that can help adjust your inventory management approach across purchasing, production, and fulfillment. Tracking key metrics can help evaluate inventory turns, identify slow-moving inventory that needs price reductions, determine optimal reorder points and order quantities, and more.
Adopting best practices enables data-driven decisions to continuously improve inventory operations. Real-time inventory tracking through modern technology solutions further enables smart, data-based management.
Improve customer service
Correct demand forecasting, combined with optimal safety stock levels, ensures there is enough inventory on hand to fill customer orders and reduce stockouts. When orders cannot be fulfilled in a timely manner, insufficient inventory results in out-of-stock items, resulting in lost sales opportunities and customer dissatisfaction.
Maintaining appropriate levels of inventory enables rapid production and increases customer satisfaction and loyalty.
Improve efficiency
Implementing standardized processes such as batch tracking, unique SKU numbers, and automated identification and data capture can streamline warehouse workflow and inventory management operations.
Automated and optimized warehouse layouts significantly reduce the time employees spend on routine inventory maintenance, stocktaking and picking activities. Employees freed from repetitive manual tasks can focus their time and energy on value-added activities.
Identify gaps and areas for improvement
Performance metrics generated by automated inventory management software highlight specific processes that may need enhancement or refinement. Detailed data analysis facilitates a fact-based review of current practices throughout the inventory lifecycle to identify issues, gaps, and opportunities for improvement.
Management can then use actionable insights to take timely corrective action when needed. Continuously evaluating and enhancing inventory management practices can maintain optimal performance over time.
in conclusion
Simply put, implementing inventory management best practices is critical to efficient business operations, optimal resource utilization, and improved profits. It is important to maintain adequate inventory levels and implement robust processes.
The 10 inventory management best practices covered in this article provide a solid foundation for evaluating and improving your current inventory management methods. While specific techniques may vary, adhering to these core principles can lead to smooth inventory operations.
EZOfficeInventory – the leading inventory management software
EZOfficeInventory provides a powerful, cloud-based solution for efficiently managing inventory across procurement and usage. It provides comprehensive inventory tracking, costing, and reporting capabilities in an intuitive, mobile-friendly interface. EZOfficeInventory seamlessly integrates with popular e-commerce platforms, accounting solutions, and barcode scanners for a unified system. You can gain real-time visibility into inventory status anytime, anywhere while minimizing management costs.
Frequently Asked Questions (FAQ)
Why is real-time inventory tracking important?
Real-time inventory tracking is important because it provides up-to-date visibility into inventory levels throughout the inventory lifecycle, allowing informed decisions to be made to avoid stockouts or overstocking. Real-time data allows for dynamic adjustments to procurement, production and fulfillment. It also improves customer service through inventory accuracy and order status visibility.
What are the benefits of accurate forecasting in inventory management?
Effective inventory management requires accurate demand forecasting. With modern inventory management tools, accurate forecasts of expected sales can better align inventory policies with demand forecasts.
Quality demand forecasting enables companies to precisely adjust and control inventory to optimize revenue. They also provide critical data to improve the efficiency of planning and inventory control.
What are the best inventory management tools?
EZOfficeInventory is a cloud-based inventory management software designed to serve businesses of all sizes. With support for multiple warehouses, barcode scanning, inventory forecasting tools, purchase order automation, mobile access, and sensible pricing plans, EZOfficeInventory is one of the top inventory optimization tools.