The operations office involves many aspects – from operational activities to decision-making. However, if the office is not equipped with adequate supplies, activities cannot continue or may be hindered, making inventory management an important aspect of business success.
Office inventory management requires tracking supplies, consumables, and valuable assets to ensure seamless execution of daily tasks. This process can get quite complicated when multiple office locations are involved. Inaccurate office inventory management can slow down operations and drain capital. A powerful office supplies management system can help increase profits, increase efficiency, and cut costs.
This article delves into the precise definition of office inventory, explains the importance of staying on top of your inventory, and provides 10 practical tips for organizing and tracking your inventory.
What is office inventory?
Office inventory refers to materials and supplies used to support office operations. It includes raw materials, maintenance supplies, work-in-progress and finished goods.
Effective inventory control means having a process for tracking inventory levels, reorder points and usage. The goal is to maintain enough inventory without tying up too much capital. With good management, workplace inventory can improve business productivity and operational efficiency.
Types of office inventory
There are 4 main types of office inventory, including:
raw material
Raw materials are supplies that are used up regularly in the office. This includes basic items like paper, pens, printer ink, batteries, and sticky notes.
Keeping an adequate inventory of raw materials prevents them from running out, slowing down work. For example, if a printer is out of paper, employees cannot print until more paper arrives. Monitoring inventory levels of supplies like paper and ordering more items before they run out can keep things running smoothly.
Repair and overhaul inventory
MRO stands for “maintenance, repair and operations” inventory. This includes spare parts, tools, hardware, light bulbs, paint, cleaning supplies and anything needed for facility and equipment maintenance. For office-based businesses, MRO inventory allows employees to make small repairs without always having to hire a contractor. Keeping MRO inventory organized means team members can find items quickly. For example, facilities staff can replace a burned out light, while IT staff can use spare parts to perform computer repairs. Adequate MRO inventory prevents costly job delays.
Work in progress inventory
WIP or work-in-progress inventory represents projects that are being worked on but not yet completed, such as presentations, reports, and proposals that are still being written. Monitoring the WIP inventory provides insight into what is currently being developed and its estimated timeline.
This allows for better planning and avoids unexpected delays. For example, check WIP inventory to ensure sales materials are finalized for next week’s meeting.
Finished goods
Finished products include final products ready for distribution, such as printed materials, bound reports, and client presentations. Maintaining adequate inventory of finished goods to fulfill regular orders and emergency requests.
For example, marketers can send brochures to potential customers immediately because newly printed copies are in stock. Finished products also include custom office supplies such as preprinted letterhead and promotional items.
Benefits of effective office inventory management for your business
Inventory optimization can increase revenue by 20%. This is especially likely to happen as unnecessary costs of trying to maintain inventory levels and warehouse space are controlled. Here are some ways you can improve your profits by implementing a strong office inventory system:
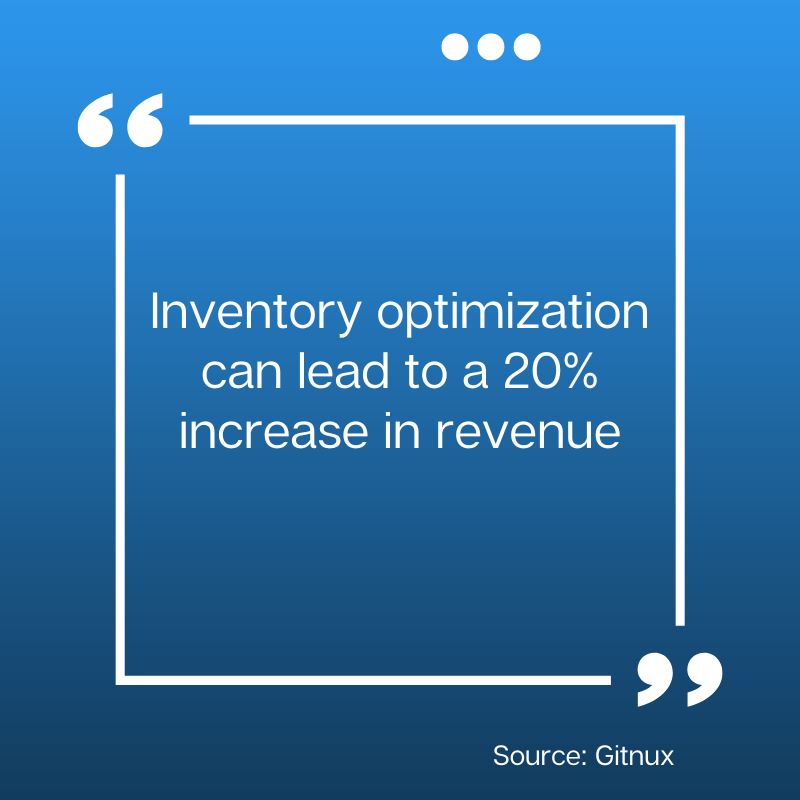
1. Save costs
Effective inventory management can lead to significant cost savings for businesses. Thoroughly tracking current inventory levels can help avoid overpurchasing items in stock. Reducing stockouts and overstocks can reduce inventory costs by 10%.
Additionally, proper storage techniques and first-in-first-out (FIFO) rotation can extend the shelf life of products and reduce losses due to expiration and obsolescence. Strategically replenishing inventory based on monitored usage trends can also prevent emergency reordering with high shipping costs.
2. Improve efficiency
Effective inventory management increases employee productivity by increasing operational efficiency. Organizing inventory storage according to logical layout, labeling, and binning minimizes search time so workers can quickly find and retrieve needed items.
Continuous cycle counting helps provide real-time visibility into current inventory availability and movement. Armed with this information, workers can focus on critical tasks rather than disrupting the workflow of procuring supplies. These practices streamline inventory accessibility and visibility, resulting in smoother operations.
3. Data-driven decision-making
Consistent inventory analysis generates the reliable data needed for insightful decisions. Tracking granular usage rates and patterns enables accurate demand forecasting while tracking key inventory KPIs. This drives data-based decisions around optimal inventory levels and ideal reorder points to avoid excessive waste.
Examining usage trends over time also supports capacity planning for future expansion needs. Instead of guesswork, powerful inventory analysis gives decision-makers confidence.
4. Regulatory Compliance
Effective inventory control helps comply with regulations in an efficient manner. Designating storage areas specifically for hazardous materials and taking appropriate precautions can simplify the process of handling these items safely and legally. Routine inspections verify consistent compliance with prescribed containment procedures.
Detailed usage logs enhance traceability and accountability for regulated inventory items. Together, these practices promote workplace safety while reducing the risks associated with noncompliance.
Top 10 Tips for Effectively Managing Office Inventory
Building an effective inventory management system requires diligence but can pay off through cost savings, increased productivity, and insightful data.
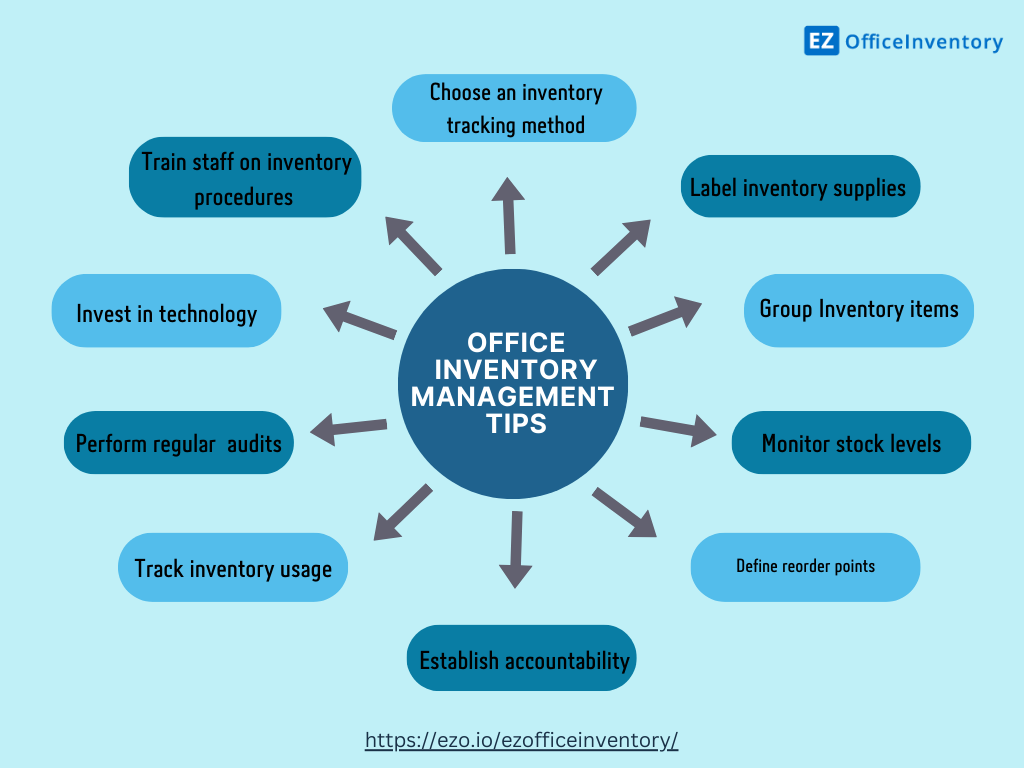
Here are 10 tips for improving office inventory control:
1. Select your inventory tracking method
Choose an inventory tracking method that fits the size and needs of your business. For small offices, simple options such as pen and paper or spreadsheet journaling may be enough.
Larger operations may benefit from a barcode scanning system or dedicated inventory management software to automate tracking.
2. Label inventory supplies
Create visible, scannable labels for all inventory items that clearly display key details needed for identification and tracking. This includes product name, SKU or part number, quantity, manufacturing or expiration date, storage requirements, and any other important information.
Use large, clear text and consistent label formatting across all inventory for smooth tracking.
3. Group inventory items
Arrange inventory items on shelves and storage areas based on logical groupings, such as supply type or function. For example, put all paper products in one area and cleaning chemicals in a separate area.
Strategic grouping makes it easier to find needed items for retrieval and makes counting during audits easier.
4. Monitor inventory levels
Designate a person to regularly count on-hand inventory quantities and record amounts. Track levels of high-usage consumables on a daily or weekly basis, while monthly inspections are less frequent for slow-moving spare parts and MRO.
Monitoring lets you understand usage and consumption rates so you can reorder before you run out of stock.
5. Define reorder points
Analyze historical usage rates and changes, expected lead times, and seasonal or projected demand changes to define the minimum quantity point for reordering each item.
Consider a buffer level above the expected minimum. Linking reorder points to data ensures that adequate inventory levels are maintained without holding too much stock.
6. Create accountability
Document authorized personnel who are allowed to access and remove warehouse inventory. Withdrawals require login and manager approval.
Record all inventory movements via a custody transfer form or tracking system, capturing details such as item, quantity, date, usage and user. Compare withdrawals to usage logs. Regular audits ensure accountability and identify discrepancies promptly.
7. Track inventory usage
Record every inventory item removed from the warehouse along with key details such as type, quantity, purpose, date and name of the person who removed it.
Capturing this usage data enables understanding of consumption and demand patterns. This drives replenishment planning and identification of fast/slow moving items.
8. Conduct regular inventory audits
Conduct a comprehensive physical inventory audit monthly or quarterly by counting all items on hand and comparing to inventory records. Investigate and document any discrepancies between recorded balances and actual amounts found.
Update inventory records and systems based on audit results. Rigorous auditing ensures accuracy and timely identification of losses.
9. Invest in technology
Utilizing dedicated office supply inventory management software can significantly improve the efficiency of managing office inventory.
Features such as real-time tracking, automated purchasing and reordering, accounting integration, and data analytics provide optimized inventory control. While technology investments come with some upfront costs, the long-term benefits and cost savings often outweigh the initial expense.
10. Train employees on inventory procedures
Train all personnel involved in the inventory process on appropriate protocols appropriate to their role. Provide initial and ongoing refresher training. Provide warehouse teams with detailed training on office supplies inventory software and protocols, while a general overview may be sufficient for casual users such as facilities staff.
Explicit training ensures consistent compliance with prescribed inventory procedures.
in conclusion
Effectively managing office inventory requires diligence, but the rewards in cost savings, efficiency and insight are huge. The strategies outlined in this article can help any organization succeed through tighter tracking, structured processes, and leveraging data. Start by critically evaluating current practices to identify gaps and weaknesses. Then build a comprehensive inventory management process that matches the size and needs of your operation.
The goal is to optimize ordering, storage and accountability, transforming inventory from a headache to a strategic asset that increases productivity.
Frequently Asked Questions (FAQ)
1. What is a workplace inventory?
Workplace inventory refers to the physical goods, assets, and materials owned by the company, such as office supplies, furniture, equipment, and documents.
2. What are the four types of office inventory?
Office inventory can be divided into four broad categories: raw materials, MRO inventory, WIP inventory, and finished goods.
3. What is the main purpose of inventory?
A key purpose of inventory is to avoid stockouts and lost sales by having enough stock to meet demand.
Effective inventory management aims to achieve balance. You need to have enough supply to meet demand, but not so much that it is wasteful or expensive to store. The key is to have the right amount of inventory in the right place at the right time.